After getting a black eye over ineffective screening and then engaging in what amounted to a work slowdown, TSA may once again be providing us in the service operations field a good teaching example. They have recently announced that they will be requiring passengers to remove all larger electronic items from their bags to be scanned.
Why the Change in TSA Service Design, especially its Scanning Procedures?
The reasons for this change make some sense from a security screening perspective.
- When a bag contains a mess of electronic gear, the scanning agent can’t really see what’s in the bag, leading to a manual bag check. (Supposedly, the advent of CT scanners that provide 3D images will obviate the need for this new procedure.) Electronic gear is a potential place to hide contraband.
- The scanning process currently is the bottleneck. The bottleneck – think highway traffic flows – is the process step that is the slowest and thus slows the whole process down. It determines the capacity of the operation, which in this case should be measured as the number of passengers processed per hour.
- Attacking the bottleneck with these new steps should speed up processing and thus increase capacity.
But will it?
The Nature of Bottlenecks
A truism of operational analysis is that you never eliminate bottlenecks; you just shift them. When you “break a bottleneck” by speeding up that slowest process step, some other step now will be the slowest.
So, with the new procedure implemented the questions for TSA are:
- What will now be the slowest step and thus the new bottleneck?
- What is the TSA doing to mitigate this new bottleneck?
- Will the new bottleneck be a worse bottleneck than before due to change in tasks in the overall process?
Here I’ll suggest what is likely to happen. No, I haven’t done any hard analysis, that is, an actual time-motion study, since I’d likely be arrested if I tried. But having observed the screening process as a frequent passenger-worker, I have a pretty good sense of the dynamic of this queuing system.
(Notice I’ve been using the term “passenger-worker.” Why? Because in any service operation, the customer has tasks to perform. Think about a supermarket. You have to choose your items, bring them to the cashier, put them on the belt, pay for your purchase, and wheel it away. Those are your tasks in the workflow. Similarly, in TSA screening, the passenger is a worker who has many tasks to perform. The passenger job design should get the same scrutiny as the blue shirt TSA agents’ job design. It doesn’t.)
Changes to the Current TSA Process Flow
Consider the nearby high-level process flow for the screening process.
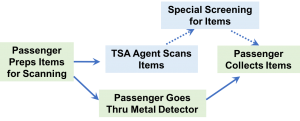
In order to speed up the x-ray screening, passengers will have to remove all electronic gear larger than a phone. The goals are to:
- Reduce the agent scanning time since the agent will have a clearer picture – literally – of what’s in the bag.
- Reduce the need for special screening, which also speeds up the initial scan since the agent won’t have to physically pull flagged bags and wait for a blue shirt to take the bag away for special screening
Impact on the Passenger-Workers
However, this process redesign assigns more work for the passenger-workers. Now, when they prep their bags for the scanner, the passenger-workers have to take out more items. That takes more time. Also, this will require more of those delightful trays that always seem to be in short supply and inconveniently placed.
Most importantly, the passenger-worker will also require more work space in the prep area for the expanded number of trays needed. To use a manufacturing analogy, the passenger-worker “work station” will now be physically larger. Today the linear space needs are for a rollerbag, a “personal item” (e.g., backpack), 1 tray for a laptop and a second tray for shoes, coats, etc. Now, add 1, maybe 2, trays for all this new stuff to be removed.
With a “longer” work station, fewer passenger-workers will be able to prepare their stuff simultaneously. That is, maybe 2 passengers will be able to prep their stuff concurrently, whereas before maybe 3 could. It’s entirely possible that the scanning agent will be waiting for the passenger to finish their prep and push their stuff into the scanner. (Goodness knows we can’t have a TSA agent actually help here by pushing stuff into the scanner.) The number of passengers processed per hour in the prep will drop, perhaps considerably.
Let’s assume passengers learn how to prep faster such that the scanning agent is not idle. However, once the stuff goes through the now-faster scanning process, the passenger-worker will have more work collecting their more disparate stuff. The scanning agent may have to pause while the passenger-workers collect their stuff, reducing some of the efficiency gains at the scanning stage. (Yes, efficacy — the quality of the scan — will hopefully still improve.)
This isn’t pie-in-the-sky theory. In Boston Logan Terminal C where an output area is physically smaller due to a post, the screener has to pause for this reason. More trays will have the same impact for a “normal” collection area – and it’s always crowded back there, especially if a passenger has been called aside for a bag to be deep screened, leaving his trays to pile up. And why can’t some of the SABSs (Standing Around Blue Shirts) collect the empty trays?
Redesign of Passenger Work Flow
Is TSA going to do anything to address the heightened passenger-worker task load? There’s no mention of it. And that’s because TSA seems oblivious to the fact that the passengers are also workers with assigned tasks.
You can be sure that the ergonomic design of work stations for the unionized TSA agents has been studied – as it should. But what about the passengers and their work areas? (Imagine if passengers could complain with a collective voice…)
Think about your typical frustrations as a passenger going through screening. The person in front of you isn’t really clear on the process and doesn’t slide their stuff down the rolling racks or tables so that the next person (you) can start his work tasks. He doesn’t push his stuff into the scanner so it just sits there.
You can’t really blame these passengers. As a work station design, the preparatory area and the collect-your-stuff area – are terribly designed. We have to pull stuff out of our bags, partially disrobe, grab trays, load the trays, and slide them simultaneously all while having someone bark orders at us like we’re some miscreants.
If this were a factory, the passenger-workers would go on strike over every aspect of the poor work design: the equipment provided, the lighting, the noise, the supervisory instructions, the blame-the-passenger-for-failure attitude, etc.
Now that problem will be even greater.
Apply Lean Concepts to the TSA Service Design
What needs to be done? The “work stations” where passengers prep their stuff and then collect their stuff need to be redesigned to improve flow time and to improve work conditions.
Think about all the unnecessary motions you expend as a passenger-worker doing your tasks. That’s waste or muda (in the Lean lexicon). And in an environment that creates muri (stress from excessive requirements).
Immediately after 9-11 we all understood the need for tighter security and that the system would be make-shift initially. 15 years later, it’s still make-shift. Put out a bunch of tables and stack some trays nearby. That’s about how much thought has still been put into passenger work stations design.
TSA seems to understand this – finally. Some airports have implemented a new work station design for this step so that multiple passengers can simultaneously prep their stuff. Bravo!
Why did it take TSA so long to actually study this aspect of the work flow – the work that the passengers perform? Any of my operations management students could have told them that. It just takes simple observation and the ability to recognize problems.
What’s the status of the new passenger work stations? Supposedly, 60 were to be rolled out by the end of 2016. Were they? As of August 2017, I have not encountered one — except in Dubai.
Um…
Oh, you say there’s not enough space for these systems at all airports? Why not? Most security areas have been redesigned and expanded since 9-11. Why didn’t the designers build in extra space – or redesign the passenger work areas as part of that redesign?
Maybe this is all part of the plan to entice people to sign up for TSA Pre-Check, which will not have to do these extra steps?